Data Sheet 16: How to Calculate Stretch in Cylinder Tie Rods
The amount of stretch (elongation) in mechanical members under tension is very easy to calculate with a simple formula. The method described on this sheet can be applied to any structural member subjected to stress. In fluid power design, it can be applied to determine the elongation of cylinder tie rods when the cylinder is under fluid pressure and is mounted as in Figure 1, or when severe momentary shocks pass through hydraulic lines; it can be used to find the expected stretch in bolts holding a component to a manifold, holding SAE flange unions together, or holding a pipe flange to the body of a hydraulic component. It can be used to estimate whether the tie rods or barrel of a foot mounted cylinder may distort under pressure, binding the piston.
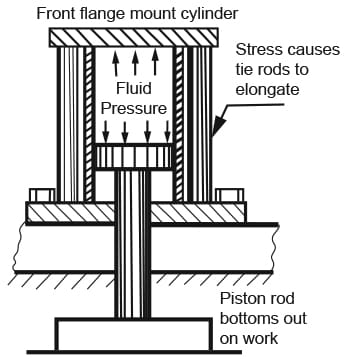
Figure 1. Tie rods elongate under fluid pressure on cylinders mounted in this manner.
Modulus of Elasticity for Common Metal (in Tension) | |
Material | Modulus of Elasticity, E |
Aluminum | 10,000,000 |
Brass | 15,000,000 |
Cast Iron, Gray | 12,000,000 |
Copper | 17,000,000 |
Magnesium | 6,500,000 |
Monel | 26,000,000 |
Nickel | 30,000,000 |
Phosphor Bronze | 16,000,000 |
Steel, Carbon | 30,000,000 |
Steel, Stainless | 28,000,000 |
Gathering Data for the Calculation
Collect the following data and you will be ready to make the calculation: (1), length of the stressed member, in inches; (2), cross sectional area of the stressed member, in square inches; (3), total applied force, in lbs., which is stretching the member; and (4), the modulus of elasticity, E, of the material from which the stressed member is constructed. This can be found from the table under Figure 1. For other materials, refer to a machine handbook. Since the modulus of elasticity is a ratio, it has no units.
Simple Formula for Calculating Elongation
Elongation = (1 × F) ÷ (A × E), in which:
L is length, in inches
F is applied force, in lbs.
A is cross section, square inches;
E is modulus of elasticity (from table)
Elongation will come out in inches.
Calculation Example for Cylinder Tie Rods
Problem: Find the stretch in the tie rods of a 6″ bore cylinder operating at 3,000 PSI. There are four steel tie rods of 1″ diameter, and they are 27″ long.
Solution: First, get all your facts assembled: Piston area of a 6″ bore cylinder is 28.27 square inches. The tie rods are the stressed members, and each rod has a sectional area of 0.785 square inches, or a total of 3.14 square inches for all rods combined. The stressing force is 3,000 PSI × 28.27 = 84,810 lbs. Modulus of elasticity is 30,000,000 (from table). Now apply the formula:
Elongation = (27 × 84,810) ÷ (3.14 × 30,000,000) = 0.0243 inches
How to Check for Over-Stressing
The stressed member will return to its normal length after the applied force has been removed provided it was not stressed beyond its elastic limit. To determine if a given force will over-stress a structural member, take the force value, in lbs., and divide it by the cross sectional area, in square inches, of the member. This will give the stress value in PSI (lbs. per square inch). Compare this with the elastic limit of the material as published in machinery handbooks. As in all mechanical design, a suitable factor of safety should be allowed.
How to Calculate Stretch Produced by Hydraulic Shock
Pressure surges which pass through the system, even momentarily, may over-stress and damage cylinders or other components. These pressure surges are generated when a 4-way directional valve is shifted, when a hydraulic motor is stopped too abruptly, when a hydraulic cylinder is allowed to de-compress too rapidly, and by mechanical shocks or impacts against the cylinder piston rod from the load. The peak pressure of these surges can be determined by instrumentation. Sometimes they can be measured by the simple method described in Data Sheet 14. Then, the above method can be applied, and the member can be checked for possible over-stressing.
Short Stroke Cylinders with Long Connecting Lines
Certain problems may develop when a short stroke cylinder is operated through long lines from its directional control valve. If the internal volume of the cylinder is less than the volume in the connecting lines, the fluid in the line is never replaced by fresh fluid coming from the supply. It circulates back and forth between the lines and the cylinder. This may be a problem in either air or hydraulic systems.
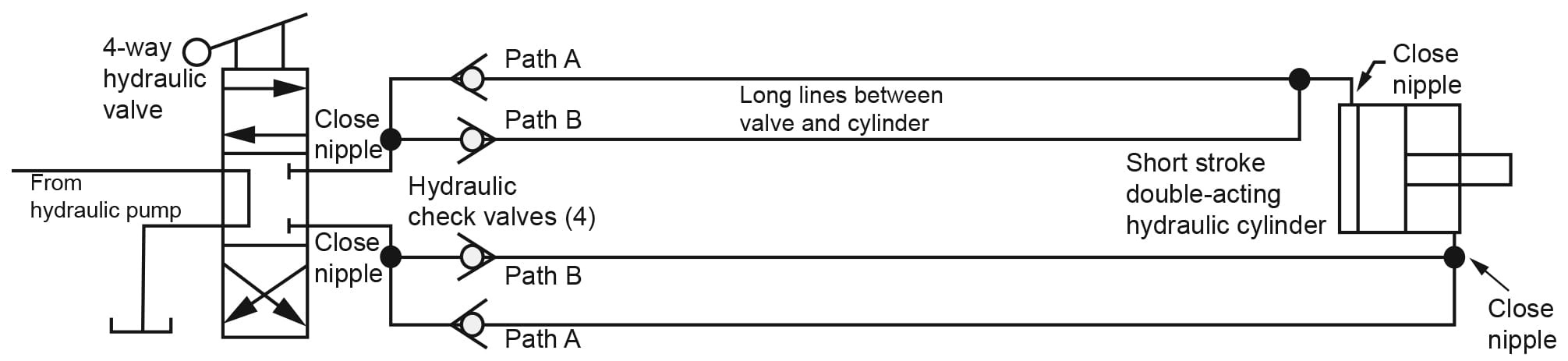
Figure 2. Replenishment of oil in lines connecting valve to hydraulic cylinder.
Figure 2. Hydraulic System. Oil which may circulate back and forth between lines and cylinder without being replaced may become overheated if cycling is rapid and regular. Hot oil causes seals and hoses to fail prematurely. There may also be a danger to personnel who may accidentally touch the cylinder or the overheated lines.
This circuit eliminates the problem. Double lines are used to both the rod end and blind end ports, isolated with check valves. Oil flowing toward the cylinder follows Paths A, and oil returning from the cylinder follows Paths B. Since the check valves prevent the oil from reversing, a new charge of oil enters the cylinder loop on every cycle.
The idea for this method: came from Fred Miner and Jerry Snow in Hydraulics and Pneumatics magazine.

Figure 3. Quick exhaust valves allow oil mist to be carried into air cylinder.
Figure 3. Air System. Short stroke air cylinders may also be a problem, but for a different reason. They are not likely to overheat, but the oil mist delivered by the lubricator in the system may never reach the cylinder, which may result in a shortened cylinder life.
Double connecting lines with check valves as in Figure 2 can be used with good results, but quick exhaust valves may be a better solution. Figure 3 shows two quick exhaust valves, although one may be sufficient. Wipe-off inside the cylinder may provide lubrication to the entire cylinder barrel.
As in any air system excess oil mist is blown out the exhaust and may contaminate the atmosphere. Lubricator feed rate should be very low, as in most systems very little oil is needed. Under-lubrication is better than over-lubrication.
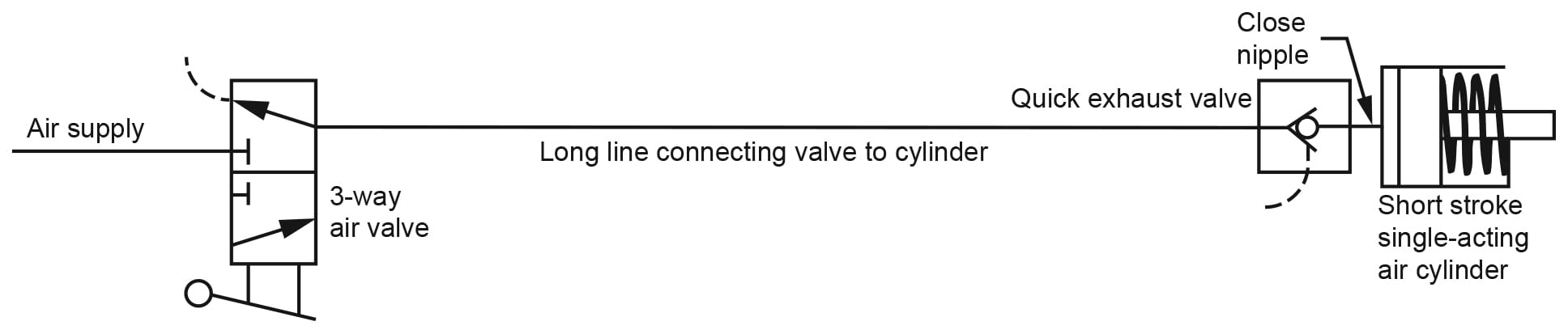
Figure 4. Single-acting air cylinder.
Figure 4. The quick exhaust method is also applicable to single-acting air cylinders for keeping the barrel lubricated. Faster cylinder retraction is an added bonus.
Note that the meter-out method of speed control cannot be used in quick exhaust circuits. Nor can needle valves be installed in valve exhaust ports for speed control. If a speed control should be needed, install a needle valve in the air supply line, or, install a meter-in flow control in the cylinder line just as close to the cylinder as possible.
© 1989 by Womack Machine Supply Co. This company assumes no liability for errors in data nor in safe and/or satisfactory operation of equipment designed from this information.